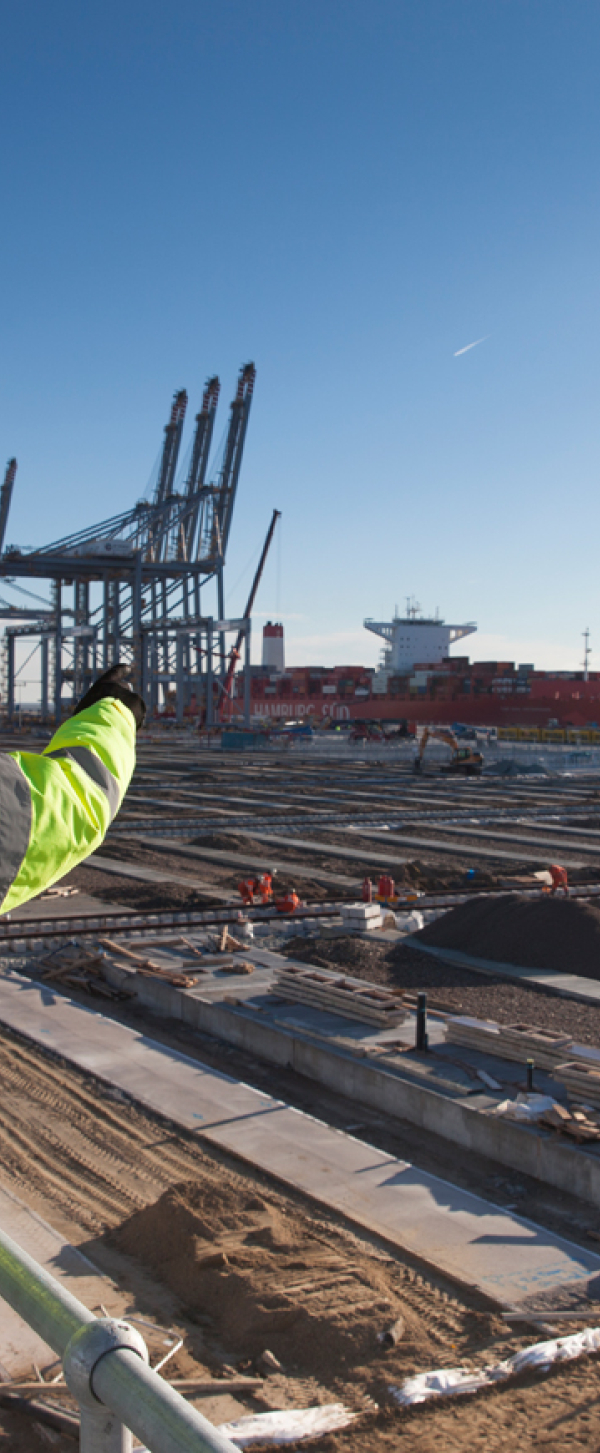
London Gateway Berth 3
VolkerFitzpatrick constructed a third berth at the UK’s new deep-sea hub port, 25 miles from central London. The construction of this berth enables the use of an additional 400m of quay, dredged to a depth of 17m, providing a stacking area for up to 10,000 containers.
VolkerFitzpatrick delivered the civil and electrical works to support the operation of four rail mounted quay cranes on this new berth.
This was an extremely high specification project on a relatively small site with an especially short program. Logistics, quality assurance and planning were essential in the successful delivery of this project.
Works commenced in January 2015 with an extensive earthworks programme to prepare the ground for approximately 1,800 container plinths to form the container stacking area.
Alongside the installation of the plinths, a vast array of additional works were completed including the construction of 1,750m of surface water drains, laying of 1.5km of rails for the gantry cranes as well as the building of electricity substations and laying of around 20km of related electrical and communications cables. The team also erected the steel reefer gantries, structures that provide power to refrigerated containers as they are loaded and unloaded onto vessels.
In October 2015, the first stage of the project was opened with the completion of the berth 7 road. This road provides access from the main port infrastructure to the new area of the port on the west of the site in advance of future development.
In preparation for the completion of the project, the team undertook around 17,000m2 of surfacing using nearly four tonnes of asphalt, laying 16,000m2 of block paving and installing an additional 3.3km of crane rails.
Environmental considerations
During the construction of berth three, 25,000 tonnes of ballast and type one base layer material was required. This amount of material would typically require over 1,200 vehicle loads if transported by road. To achieve a more cost effective and environmentally friendly solution a bulk carrying vessel was sourced to ship the material directly to the port, where it was unloaded from the ship directly onto site. It took three months of planning and extensive negotiation with the supply chain and client to execute this logistics solution. This solution saved over 70 tonnes of CO2 emissions.
Quantities:
• 6,000m3 of Pavement Quality concrete slabs
• 4.5 km of crane rails
• 1,800 reinforced concrete structures
• 20km drainage, ducting and communications cabling
• 17,000m2 of surfacing
• 16,000m2 of block paving